The research field
The department’s work involves both “upstream” research to understand thermomechanical phenomena linked to manufacturing processes (advanced machining, micro-machining, grinding, etc.) and tribological behavior under extreme conditions, as well as applied research for industrial purposes.
The two aspects of this work interact and feed into each other, combining modeling and experimentation to meet the expectations of the industrial world. Modelling is analytical, numerical or hybrid. They are multi-physical and multi-scale, integrating the thermo-visco-plastic behavior of materials, microstructure, damage, tribological conditions under high pressure, high sliding speed and high temperature, as well as wear.
The department’s experimental studies are based on four test platforms featuring instrumented machines for measuring stress, temperature, strain and vibration. As part of its projects, the department also develops its own sensors.
Advanced machining
Micro-machining
Rectification
Tribology under extreme conditions
Dynamic behavior of materials
Damage
Wear
Multi-physics modeling
Multi-scale modeling
The members
Professors and research directors
Lecturers and research associates
Technical staff
PhD students
Post-doctorat fellows and contract researchers
Guests – other staff
Research areas
Thermomechanics of advanced manufacturing processes
Coordinators: Romain Piquard and Cyprien Wolff
In this area, the department deals with the thermomechanics of shaping processes using cutting tools or abrasion. In these manufacturing processes (advanced machining, micro-machining, grinding, etc.), the materials in the part-tool pair are subjected to extreme conditions of temperature, stress and deformation rates, making analysis, modeling and simulation particularly delicate. Modeling is multi-physical and multi-scale, based on analytical, numerical or hybrid approaches. Work in this area combines modeling and experimentation, and develops original approaches to industrial problems. At the microstructure level, investigations aim to take into account the effects of material microstructure (crystallographic texture, topology and grain size, phase changes, etc.) on tool-material interaction, as well as its evolution as a function of thermomechanical loading induced by the material removal process. This area has historically focused on metallic materials, but is also developing skills in the machinability of composites, surgical procedures (cortical bone) and the finishing of parts produced by additive manufacturing (hybridization).
FEA SIMULATION OF THE MACHINING OF HONEYCOMB STRUCTURES
Honeycomb materials can be used to lighten structures, particularly in the aerospace industry. However, when these materials are machined, the walls of the honeycomb cells in contact with the cutting edges vibrate, making it very difficult to simulate material removal. We have developed a coupled experimental-digital approach to analyze their mechanical behavior during a milling operation. A behavioral model is proposed, taking into account the heterogeneity of the honeycomb structure, the interfaces between the walls and the progressive degradation of mechanical characteristics (damage, chip formation, burrs, etc.).

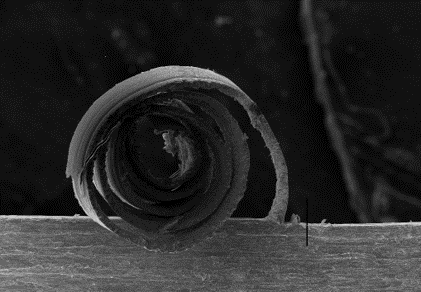
PHENOMENOLOGICAL, ANALYTICAL AND NUMERICAL MODELING OF MICRO-MACHINING
In micro-milling, cutting forces are determined by numerous parameters, including feed rate per tooth, depth of cut, angle of cut and material being machined. Due to size effects, problems inherent in the micro-milling process, such as chatter, edge radius or tool deflection, influence cutting forces, making it difficult to understand the process. Based on the development of original orthogonal and oblique micro-cutting experiments, chip formation and forces are studied with a view to modeling micro-cutting. The work also involves the development of analytical and numerical models that take into account the effect of the machined material’s microstructure.
DIGITAL ANALYTICAL MODEL FOR FA LPBF HYBRIDIZATION – 5-AXIS MILLING
Today, finishing operations on parts produced by LPBF additive manufacturing represent a major challenge in this field. To obtain a functional part, some surfaces require post-processing by machining operations. In this study, an innovative approach is developed using manufacturing supports as a clamping device for the milling operation. The aim of this study is to propose a model combining an analytical approach to determine the cutting forces with a finite element model (FEM) to predict the dynamic response of the part-support system.
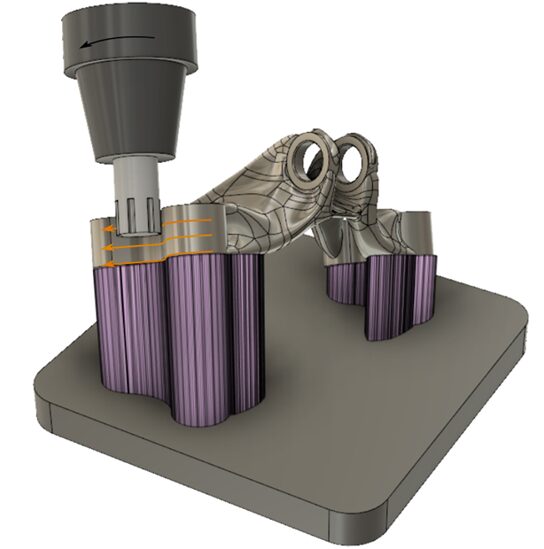
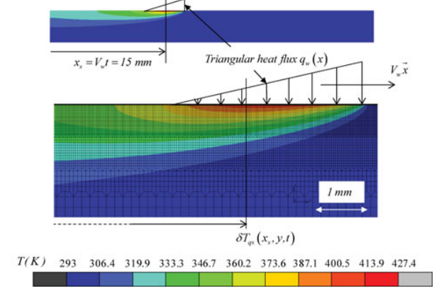
HEAT FLOW DISTRIBUTION IN SURFACE GRINDING
In this study, the average heat flux and the partition ratio are determined under grinding conditions without burning and with burning. An inverse method with an innovative sheet/workpiece thermocouple device is used to evaluate the overall heat flux distribution and the heat flux distribution in the workpiece during grinding under oil lubrication.
Extreme contact and dynamic behavior
Coordinators: Mamadou Coulibaly and Hamid Makich
Tribosystems under severe conditions – Our research activities are aimed at meeting the new requirements of tomorrow’s energy and transport industries (for which the speeds and temperatures involved are constantly increasing). Approaches are both experimental and theoretical, and focus on tribosystems operating in severe environments (cryogenic, high temperature, high speed, high pressure, etc.) for short or long contacts, open or with recycling of the third body. The multi-scale and multi-physics study tools developed by the team enable us to establish relationships between the genesis of damage mechanisms and the loading conditions imposed, taking into account interface geometry for a wide spectrum of material pairs. Finally, the dialogue between the various tools used enables them to be optimized and to complement each other in the analysis of observed results correlated with the properties of the tribosystems studied.
Tribology of machining processes, surface, interface and wear – In machining, micro-machining and grinding, the study (modeling and experimentation) of tribological conditions at tool-material contact interfaces without lubrication involves the analysis of different tribological conditions (bond-slip contact, heat exchange, dynamic recrystallization, chemical diffusion, cutting tool and grinding wheel wear, cryogenic conditions, etc.). Knowledge of the physical mechanisms governing these tribological conditions and how they evolve as a function of process parameters enables us to understand material-product-process interactions.
ADHESIVE WEAR DURING HIGH-SPEED FRICTION CONTACT
High-speed sliding friction tests are carried out by subjecting the samples to an apparent normal pressure of 110 MPa over a range of 40 to 64 m/s, in order to reproduce the severe conditions of contact between rotating blades and the rotor in aircraft engines. Consequently, impacts of a projectile against a fixed sample are carried out for the study of a pair of Ti6Al4V materials by a patented device. Post-mortem analyses of the samples reveal a breakdown of the friction subsurface into several distinct layers: initial microstructure, severe plastic deformation, phase transformation and material transfer.
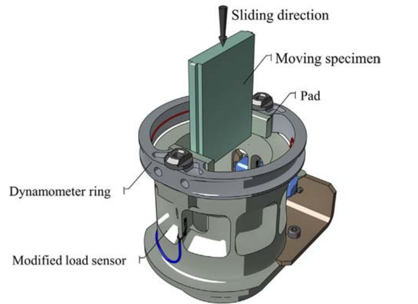
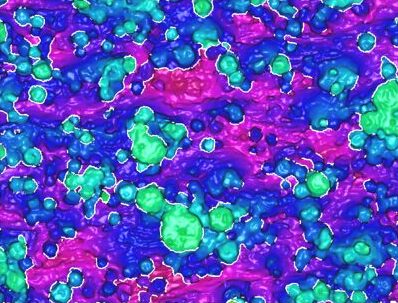
IDENTIFICATION OF CONSTITUTIVE LAW PARAMETERS FOR ABRADABLE COATINGS
Abradable coatings are part of the dynamic seals used in aircraft engines to reduce interstage leakage by reducing rotor/stator clearances in low- and high-pressure compressors. Due to the complexity of reproducing rotor/stator interactions experimentally, modeling approaches are used to optimize the choice of abradable coating. Experimental investigations include thermal measurement coupled with a high-speed camera to identify the parameters of a standard Johnson-Cook-type constitutive law for the wide ranges of strain rate and temperature explored.
FORMING THE MACHINING LAYER
This study proposes an experimental methodology to identify and describe Build Up Layers (BUL) occurring on the cutting face of the tool. Machining tests were carried out on a high-strength free-cutting steel with non-metallic inclusions, using a coated carbide tool. BUL morphology and composition were determined for different cutting conditions. Its formation strongly modifies tribological conditions at the tool-chip interface. Temperature distributions at the tool-chip interface were measured during cutting tests using an infrared camera. The appearance of the BULs was then linked to the thermomechanical conditions at the tool-chip interface.
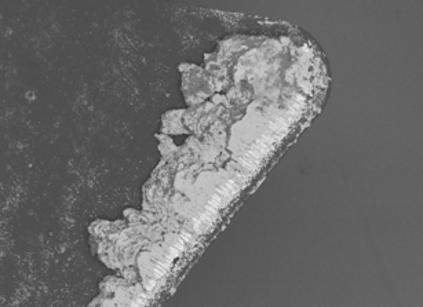
Thesis in progress
Thesis in the T-PRIOM department
Modélisation multi-échelles par élément finis du comportement hétérogène d’un matériau obtenu par le procédé de Fabrication additive SLS
Modélisation thermomécanique meso-macro de la rectification plane de profils d’aube de turbine en alliage base Nickcel
Caractérisation du chargement thermomécanique et de l’usure à l’interface outil/pièce en usinage (rectification et tournage) à l’aide de capteurs en couches minces
Analyse et modélisation du comportement à l’usure des outils de coupe à l’échelle de la microstructure
Etude de l’usure dans les contacts sous chargements thermique et mécanique extrêmes : application aux couples ‘outil-matériau’ en usinage
Etude expérimentale et modélisation du comportement de polymères chargés fibres obtenus par le procédé de FA SLS
Maintenance prédictive basée sur l’intelligence artificielle de systèmes cyber-physiques et manufacturiers : approches semi-supervisées et non supervisées
Analyse expérimentale et simulation numérique de l’usinage 5 axes sous environnement cryogénique
Analyse dynamique de l’interaction machine-outil-pièce en usinage à l’aide de l’intelligence artificielle : application au fraisage des matériaux en nid d’abeilles
Modélisation thermomécanique de l’usinage par abrasion à l’échelle des grains